选择与需求相匹配的计量解决方案是关键
尽管在生产操作中,部件检查只是整个工作流程的一部分,但是减少这一工作量有可能带来显著的投资回报(ROI),特别是在检查过程中引入自动化时。
了解公司投资回报率的关键是选择能够解决您自己特定工作流程中的瓶颈、盲点和潜在的不一致问题的检测解决方案。
数字化世界中的机械手段
“坐标测量机(CMM)和机械检测仍然被一些公司或公司内部的部门使用。” Layout Source(TLS)总裁Jeff Moore讲到。“因为有很多在机械检测方面经验丰富的技术人员正在退休并离开这个行业,因此需要采用新的检测方法。”
在考虑检查选项时需要注意的其他方面是处理从传统技术到新技术的方式转换,以及新系统的成本。精明的组织将计算数字检查与机械检测的时间节省,调查数字解决方案投资,并计算投资回报率。在大多数情况下,节省成本和提高产量的潜力远远超过过渡到数字解决方案的挑战。
机械方法缺陷和数字解决方案
尽管用于尺寸检查的传统方法在某些情况下仍然具有价值,但与3D扫描相比,使用高度计、平板和旋转台的机械检测系统很慢并且受到人为错误或偏差的影响,并且受检测人员的影响因素很大。
“在每次检测一个点时,CMMs的成本与输出比很高,而在3D成像或扫描中则每秒可以检查数千个点。”Moore解释道。“将CMM报告输出成表也会增加首件检查(FAI)的成本。CMMs适用于规格几何形状,如用于测量试样或粗糙铸件的表面时表现不佳。
Layout Source是一家质量检测公司,专门从事复杂航空铸件的首件检查。该公司使用自动化数字检测系统满足航空航天工业的高要求,与其他任何方法相比,可以在很短的时间内完成重复性首件检测。此外,生产检验可在几分钟内完成,并提供实际结果的完整数字文档。
Automated inspection solutions 80% to 90%
自动检测解决方案通常会使检测间和工作量减少80%至90%,并且具有绝对可靠的重复性。
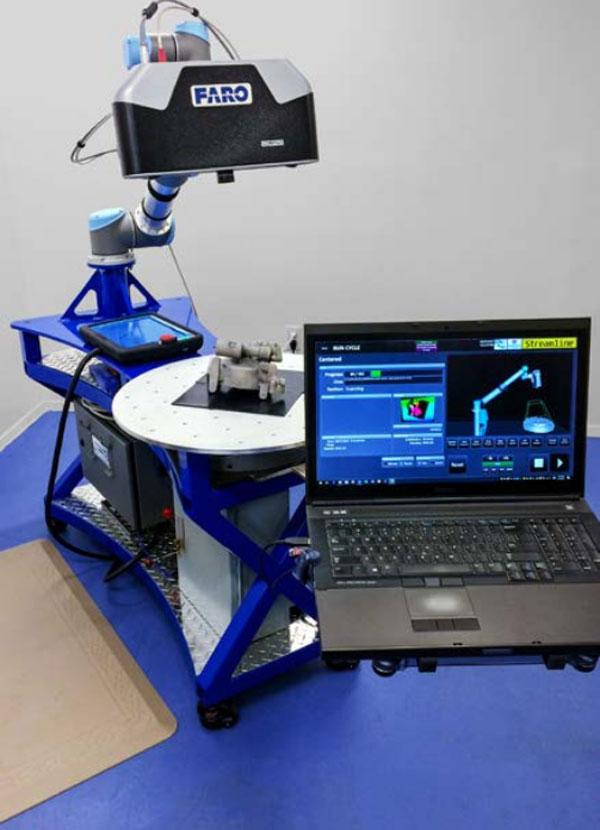
“当你生产铸件并且进行加工时,你必须依据实际铸件尺寸过大这一实际,然后在关键区域加工以获得最终部件。”Moor讲到。“我们关注的过程的一部分是它的目标控制方面。目标控制基本上是通过铸件上的关键基准点或接触点定义,操作员使用这些关键基准点或接触点在加工中心设置铸件。如果操作员无意中以微小的偏移或角度加工,您可能会加工到一个关键区域,那样该部件将成为昂贵的废料。”
换句话说,由于手动定位不像3D成像或扫描那样准确,因此在制造过程中会产生一定量的废料,需要将其考虑在内。3D成像技术,如FARO Cobalt阵列成像仪可提高工艺效率,从而减少废料,从而节省成本。
FARO Cobalt阵列成像仪是一种计量级非接触式扫描仪,利用蓝光技术在数秒内捕获数百万次高分辨率3D测量坐标。
Cobalt可轻松部署在手动或全自动工作流程中,可为工件、装配体和工具上的尺寸检测和逆向工程应用提供快速一致的测量。
Cobalt非常适用于许多行业的自动化计量应用,例如汽车,航空航天,金属加工和其他利用自动化的行业。
“Cobalt的一个非常有用功能是它允许我们改变曝光设置,”3D InfoTech(3DI)总裁Rohit Khanna说。“有时工件为光亮饰面,有时工件为哑光饰面。你可以用Cobalt处理各种各样的工件饰面。”
3D成像和扫描正在取代许多机械方法的测量,使测量更容易,并且不易出现测量错误。
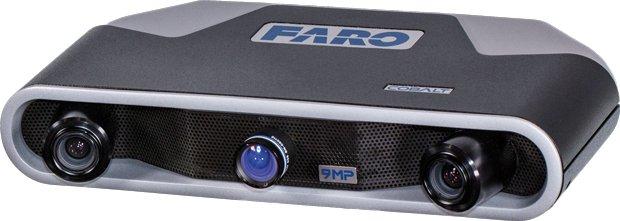
生产环境中的自动化解决方案
下一代检测解决方案是集成自动化。自动化计量系统为中到大型操作提供了多种好处 - 尤其是1-3级供应商。
一些航空航天原始设备制造商正在寻求实施生产批准程序或PPAP(100%检验),PPAP已经被汽车行业采用。要进行100%的检查,自动化对于确保一致、可重复的检查并最终保持盈利至关重要。数字检测系统通常不具备该程度的自动化,导致每个部件必须被独立检测,从而降低一致性,或必须在可编程CMM上执行该检测过程。
此外,100%检测可生成大量数据,可用于优化生产公差并有助于更好的工程设计。
“我们的想法是对每个工件进行生产检验,”Moore讲到。“这是我们和航空航天、汽车和其他制造业的许多其他人共同的目标。数据很重要。当然,我们不想最终拒绝每一个部分,但我们希望从数据中学习。正确分析的数据成为可操作的信息。这些信息允许工程师深入,分析不合格,并了解公差或改变工件检查的方式,或者找到解决数据的方法。”
简而言之,自动化解决方案在大批量检测中的优势包括节省时间、减少操作员疲劳、提高检测的可重复性。
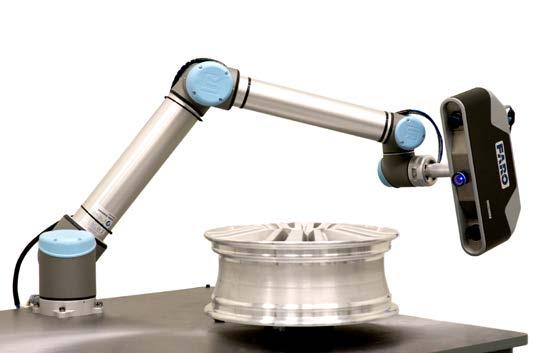
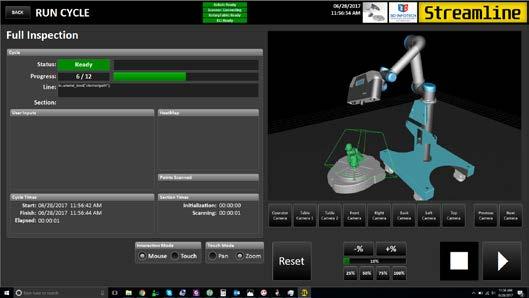
定制化解决方案
3D Infotech (3DI)是一家三维计量系统的集成商,自主研发Streamline集成软件,专注于提供所有测量流程的自动化的自动化计量解决方案,
3D Infotech (3DI)的创始人Khanna说:“我们的UMA(通用计量自动化)解决方案包括一个带扫描仪的机械人、旋转工作台和我们的Streamline软件。在UMA系列产品投入市场前,为了确保产品能满足各种检测需求,我们测试和集成了各种各样的硬件设备,各种影像仪、FARO关节臂、UR机器人等。操作员只需要把部件放在旋转夹具上,点击streamline软件中的“播放”按钮,等待测试报告完成。所有的测量数据会自动保存到CAD程序中进行查看或实时调整,必要的时候可以进行离线调整。”
3D Infotech的致力于为客户提供定制化的解决方案为己任。Khanna解释道:“我们是解决方案的提供者,为确保给客户提供最好、最有效、最有性价比的解决方案,在产品设计初期,我们充分调研客户的需求和痛点,我们的产品设计包含客户比较关注的精度需求、使用的便携性、系统的可配置性等”
“UMA背后的引擎是streamline软件。目前,我们可以连接不同品牌的机器人。Streamline可视化、触摸屏的操作界面,一键式“开始”或“停止”工作按钮操作非常简单。它与Polyworks®软件集成,自动提取检测报告。让您轻松实现一体化检测流程。”
“产品的可扩展性是客户选择我们的原因之一。如果客户想换另一个机器人,那么我们帮您实现即插即用的替换。如果客户想把测量数据连接到工厂数据库,我们也能帮您实现一个即插即用的改变。所有的客户需求都是streamline内置功能。我们的streamline软件可以直接与可编程逻辑控制设备进行兼容。”
FARO产品在3DI 解决方案中的体现
3D Infotech (3DI)的创始人Khanna说:“3D Infotech 专注于自动化计量已经超过12年,自成立以来,我们与FARO进行了合作。一直以来,该公司都给予我们很大的支持。在任何时候,对于任何问题,FARO总是积极主动地协助我们。我们信任并依赖FARO的产品和技术,他们的员工非常出色。”
“When we designed this system, we went through an evaluation phase where we looked at a variety of 3D Imagers, as well as robotic arms before we proposed the final package, which in terms of hardware, incorporated the FARO Cobalt solution with the Universal Robot.”
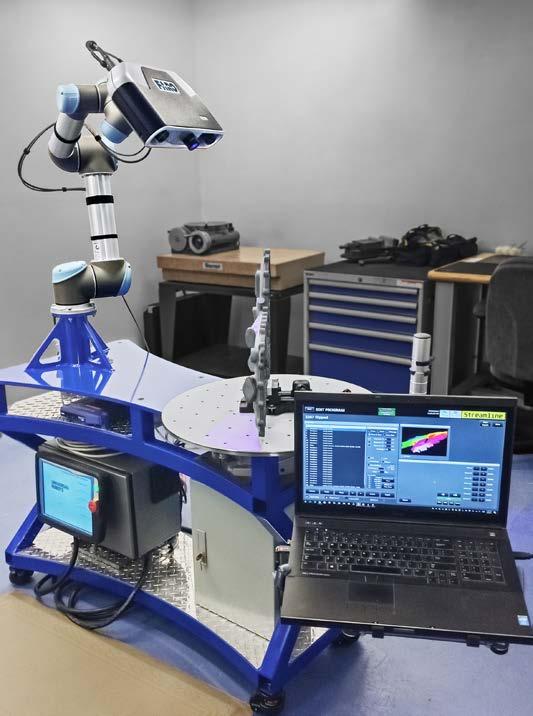
结论
自动化检测可以大大减少了检测时间和工作量。当自动化设备编程集成了机器人和Faro Cobalt扫描仪,进行首样检测后,其它部件完成自动检测,操作员的误操作不会导致检测结果的不同。机械首样检测需要8周的时间,而数字化首样检测需要5周的时间(扫描程序和检查只需几天),重复首样检测需要2.5周。对于重复性,传统方法需要20 - 60分钟,全三维自动化测量检测时间只需几分钟。通常,自动化检测解决方案可以减少80%-90%的检测时间和工作量,并且具有绝对的可重复性。
最后,每个企业需以致力于开发适应客户需求的检测解决方案为己任。非常幸运地是,市场上除了3D Infotech公司,还与 The Layout Source、FARO这样的公司一起,拥有数十年的经验,分享自己独特的见解。